Track Every Step: How Real-Time Production Line Monitoring Ensures Quality
- factrac
- Mar 26
- 5 min read

In today’s modern era, maintaining product quality is more important than ever. Quality control is not simply about testing the finished product but at the same time, it's about monitoring each and every step of the production process in real time so problems are caught before they arise. This is where real-time production line monitoring comes in.
Real-time monitoring provides unparalleled insight into production. Manufacturers have complete visibility of all steps within their operations, the ability to catch inefficiency and defects as they happen, and the immediate authority to change what needs changing. In this blog, we're going to talk about how a real-time line production line monitoring solution is implemented and why it is perfect for quality control.
What is Real-Time Production Line Monitoring?
Real-time production line monitoring software is a technology process involving sensors and software to monitor all activity and movement on the production line in real-time. It enables manufacturers to monitor machine performance, worker movement, production rates, and even environmental factors, like temperature and humidity.
The objective of real-time monitoring is straightforward and that is to allow the production process to go smoothly and any problems to be highlighted in real time so that corrective action can be taken immediately. Whether it is to detect a production flow bottleneck, detect a machine malfunction, or detect a product specification deviation, real-time monitoring guarantees that manufacturers are able to anticipate potential problems.
Detecting Problems Before They Escalate
One of the largest manufacturing challenges is catching problems early enough so they don't impact the finished product. Real-time production line monitoring solves this by continuously gathering information from all areas of the production line.
For instance, if a machine starts to run beyond its optimal limits, the monitoring system will notify operators of the issue in real time. Through this real-time feedback, operators can take corrective measures, for instance, recalibrating the machine or replacing a worn-out component, before the issue results in faulty products or expensive downtime.
By detecting issues early, manufacturers can prevent delays, reduce waste, and ensure that products are of quality consistently.
Enhancing Quality Control at Every Stage
Quality control cannot be an afterthought. It has to be built into every aspect of the production process. Monitoring in real-time provides ongoing quality control, not merely at the stage of final inspection, but through the entire process of production.
For instance, sensors implanted in equipment can track key parameters such as temperature, pressure, or speed during manufacturing. These readings are then checked against pre-established quality standards. If any of these parameters are outside the acceptable range, the system alerts the problem and prompts operators to act.
Improving Efficiency and Reducing Downtime
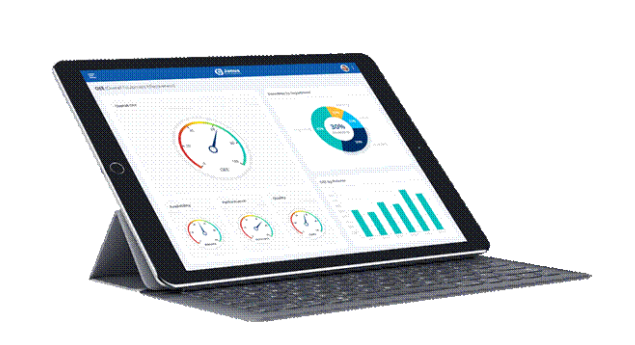
Real-time monitoring is not merely about capturing defects but also about maximizing the whole production process. By monitoring production data such as machine utilization, cycle times, and throughput, manufacturers can spot inefficiencies in the workflow.
For example, real-time tracking could show a specific machine running at less than full capacity or a production process taking longer than it should. Equipped with this information, manufacturers can alter things on the fly to increase efficiency, eliminate downtime, and overall improve throughput.
Further, real-time monitoring minimizes unplanned downtime by facilitating predictive maintenance. With real-time tracking of machine performance, the system is able to anticipate when a machine is bound to fail and plan maintenance before the breakdown takes place.
Enhancing Traceability and Accountability
One of the strengths of real-time production line monitoring is that all action taken within the production process can be followed. Whether one is a machine operator, a technician, or a material handler, each part of the process can be logged and traced.
This degree of traceability is worth its weight in gold for both internal and external audit purposes. If there is a quality problem, manufacturers are able to identify precisely where during the manufacturing process the issue arose. This not only assists with the resolution of the problem but also ensures employees are held accountable for upholding quality standards.
Traceability is also essential for regulatory compliance. Most industries, including food production or the pharmaceutical industry, need to document the manufacturing process rigorously.
Providing Real-Time Data for Decision-Making
Real-time production line monitoring offers immediate access to critical information, enabling managers and decision-makers with the data required to make intelligent decisions.
By having access to up-to-the-minute performance statistics, managers are able to rapidly determine if production is on schedule or if it needs to be corrected. For instance, if production is running behind schedule, managers are able to utilize real-time data to determine the reason for the delay and implement corrective measures.
Moreover, historical data collected from real-time monitoring can be analyzed to reveal trends and patterns in production performance.
Reducing Costs and Waste
When problems with production are identified and addressed early, manufacturers are able to cut significantly the cost of waste, rework, and scrap. For instance, if a defect is identified early in the process of production, it can be addressed before it spoils the whole batch, saving materials and eliminating the need for expensive rework.
In addition, real-time monitoring optimizes resource utilization. With real-time monitoring, manufacturers are able to see how machines are being used, labor deployed, and materials being consumed. Through this, inefficiencies can be identified, waste can be minimized, and resources can be utilized as efficiently as possible.
Better Customer Satisfaction
Ultimately, the end result of all these improvements is increased customer satisfaction. By making sure that products are always high-quality, on-time, and defect-free, real-time monitoring directly enhances customer trust and satisfaction.
Having a strong quality control system allows the manufacturers to better satisfy customers more frequently, something that is important for long-term relationships and keeping a brand in good standing.
At Factrac, we are experts at delivering real-time production line monitoring solutions that help your operations to run smoothly, efficiently, and with the highest quality standards. Our software empowers you to monitor each step of the process, avoid defects, and maintain your production lines at optimal performance.
FAQs
How does real-time production line monitoring improve quality control?
Real-time monitoring constantly monitors important production parameters and notifies operators if any variations are detected. This is an anticipatory method that enables manufacturers to solve problems before they impact product quality.
Is real-time monitoring suitable for all types of manufacturing operations?
Yes, real-time monitoring can be applied in different kinds of manufacturing operations such as assembly lines, batch processes, and continuous processes. It can be made to suit individual requirements.
How does real-time monitoring reduce downtime?
By monitoring machine operation and detecting potential wear or malfunction early on, real-time monitoring enables manufacturers to schedule predictive maintenance prior to the occurrence of a breakdown, thus reducing unplanned downtime.
Conclusion
Real-time production line monitoring is a vital resource for manufacturers looking to ensure the highest level of quality, drive efficiency, and cut costs. With real-time monitoring of each process in production, it gives manufacturers the power to identify problems before they occur, streamline resources, and make intelligent decisions. Thus, manufacturers can produce high-quality products consistently and on schedule, enhancing customer satisfaction and maximizing their bottom line.
Comments